eKSM System
In manufacturing environments, quality control processes include routine checks to verify that components used in production align with the current work order.
These inspections are carried out periodically—every few hours or multiple times during a single shift. The focus is on components installed on production machinery, ensuring full compliance with production standards and requirements.
With our electronic KSM solution, the entire process of component identification and verification becomes more transparent, precise, and user-friendly—enhancing control, minimizing errors, and streamlining day-to-day operations.
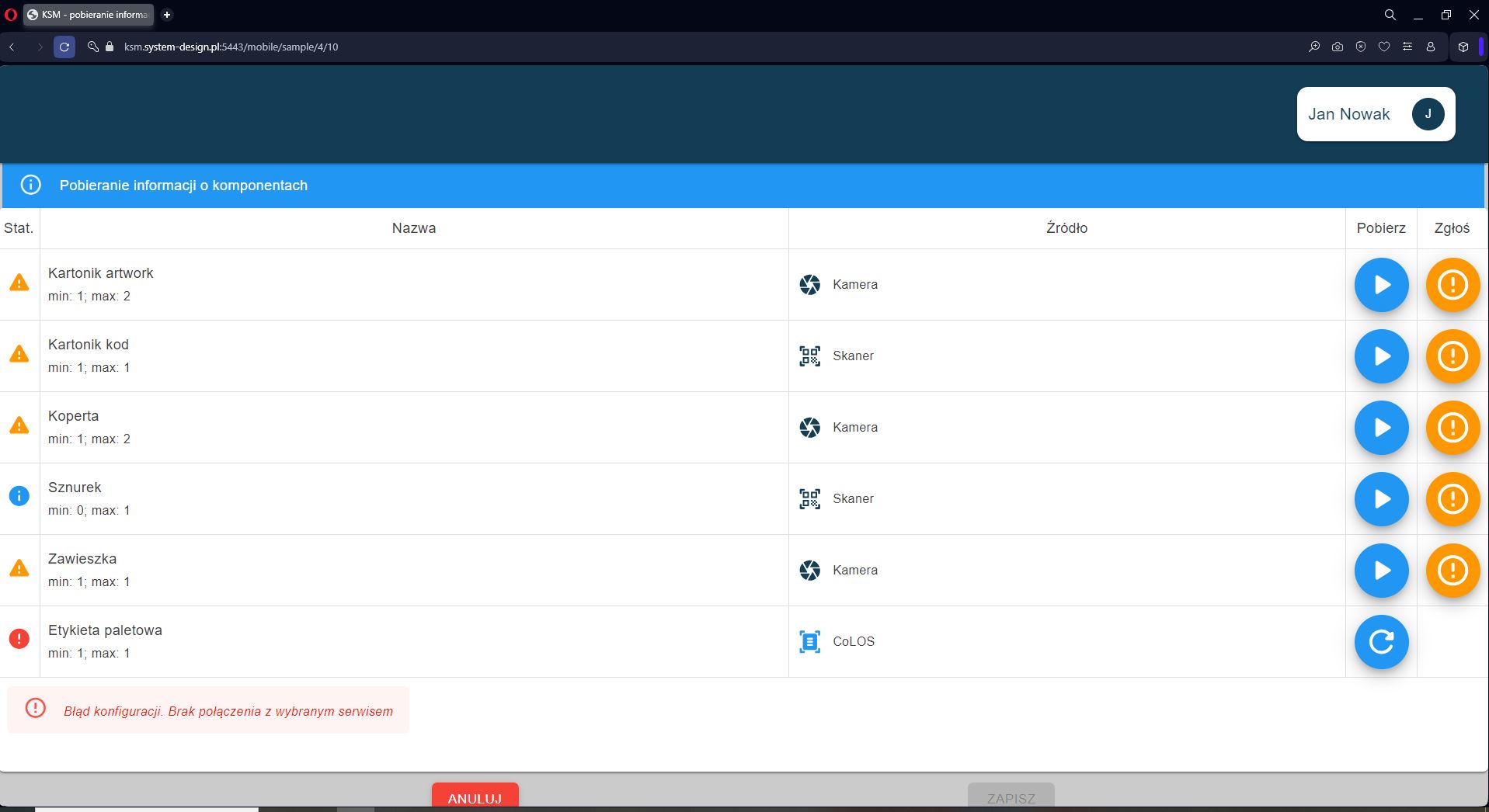
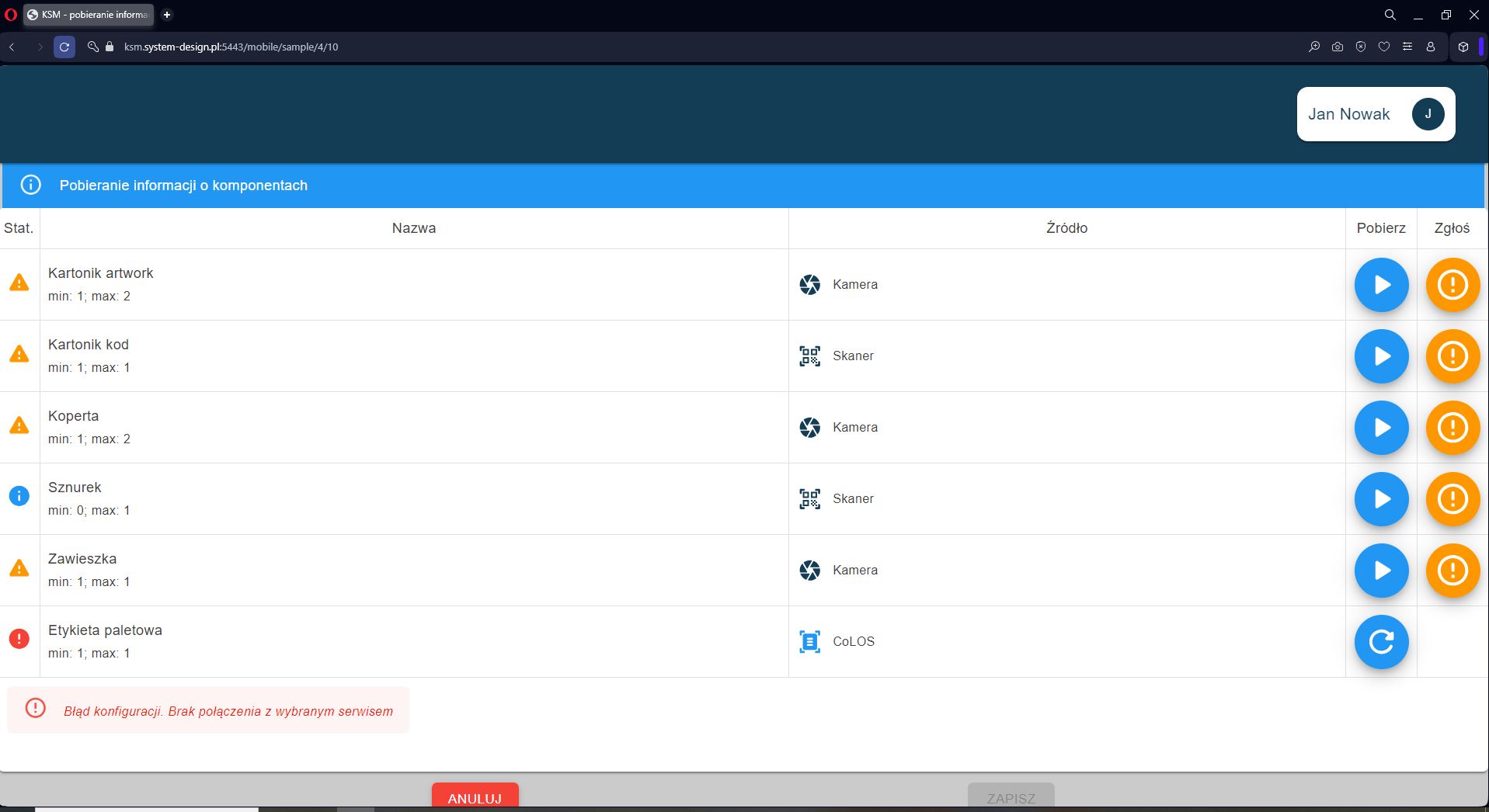
The KSM application offers two flexible data entry modes to match the specific needs of your production environment:
- Manual Mode
- Enables operators to input data using:
- Barcode or QR code scanners
- Camera or video input from mobile devices or workstations
- Manual entry of parameters directly by the operator
- Automatic Mode
Streamlines data collection through:
-
- Automatic integration with production systems like CoLoS®
- Communication via industrial OPC standards
- API integrations or connectivity with other factory systems
This dual-mode functionality ensures seamless operation—whether you're working in a digitally advanced factory or gradually transitioning from manual to automated processes.
The KSM application is a modern tool that significantly improves quality control and reporting processes in production environments, while offering a high level of flexibility and seamless integration with existing factory systems.
By eliminating the need for manual documentation, the system reduces the risk of errors and enables more efficient management of quality data—supporting smarter, data-driven decision-making in modern manufacturing operations.
A demo version is available, allowing users to explore the app’s core features, including custom report configuration. It highlights how quickly and intuitively the solution can be tailored to meet individual user preferences and operational needs.
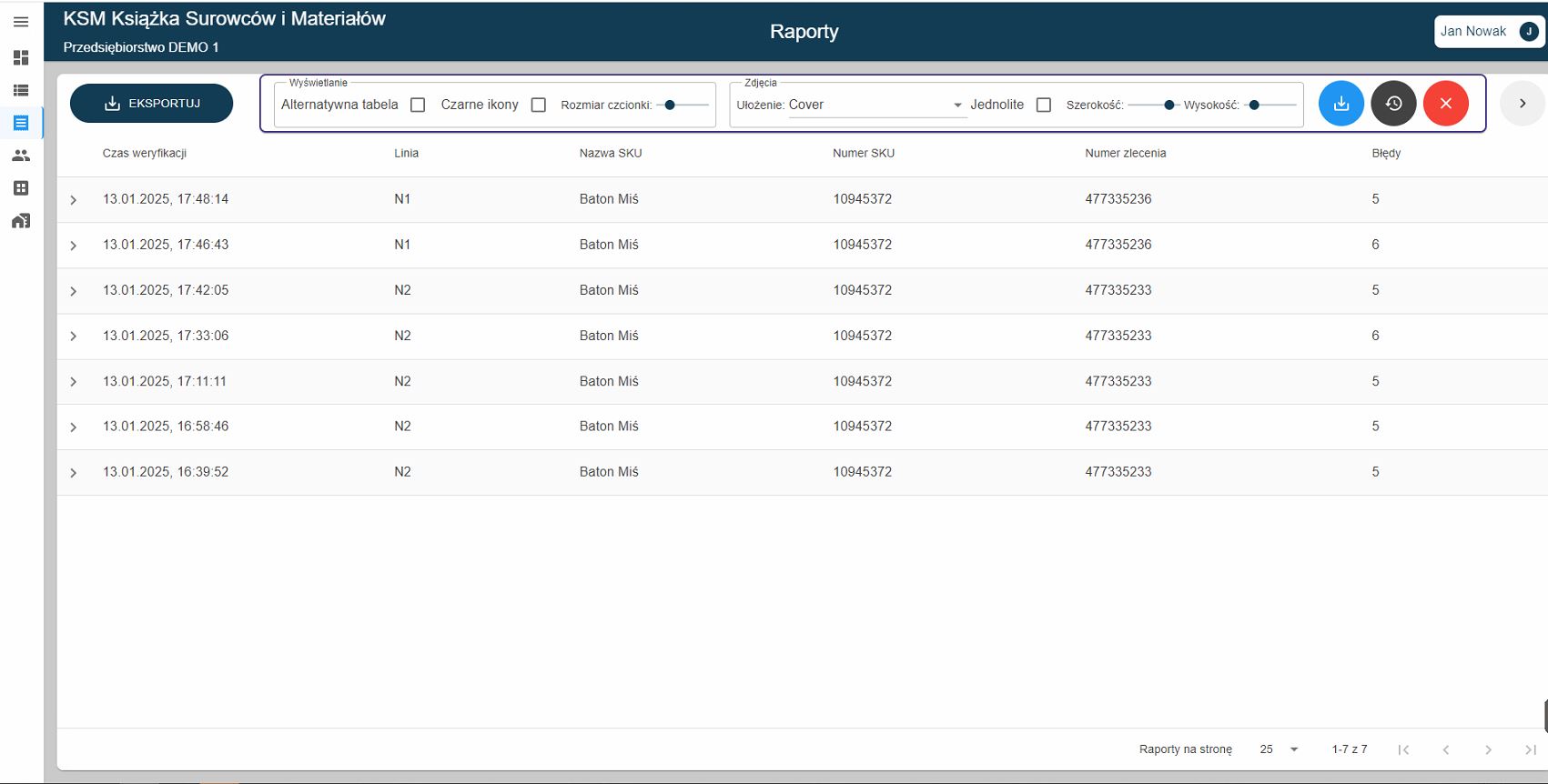
- Lower operational costs by regularly verifying production components against the current work order, ensuring alignment and reducing waste
- Greater transparency & audit readiness – All quality data is stored digitally and accessible at any time, making both internal and external audits faster and more efficient
- Improved production quality through consistent and accurate component checks, ensuring materials meet required specifications and quality standards
- Faster quality checks thanks to automated data entry and seamless integration with industrial standards like OPC—drastically reducing inspection times
- Instant nonconformity reporting – Quickly detect and respond to issues, minimizing downtime and supporting proactive quality control
-
Reduced material losses by catching mismatches early—preventing the use of incorrect raw materials and enabling faster corrective action
- Data Digitalization – All records are stored in a secure database, with each entry representing a specific action for full traceability and historical insight
- Easy Data Access – Quality teams and other departments can instantly access information on demand, export it to Excel, or integrate it with other internal tools
- MultiSite Architecture – A single central server can manage multiple production facilities, ensuring consistent system performance and streamlined operations across distributed locations
- Flexible and Configurable – The system adapts to each client's infrastructure, production workflows, and quality control processes
- Advanced Analytics & Reporting – Built-in tools for trend analysis, error charts over time, and breakdowns by production line, machine, or other variables empower the quality department with actionable insights
- No Installation Required – As a fully web-based solution, the system runs directly in a browser—no need for local installation or maintenance on user devices
Case Study
Traditional Method of Managing the Raw Materials and Components Logbook (KSM)
In companies that have not yet digitized the KSM process, a paper-based approach is still commonly used. Typically, this involves a physical notebook with pre-printed tables that are filled in manually by production operators or line supervisors. The entries usually include:
-
Production line name
-
Production order number
-
Date and time
-
Expiry date (BBD)
-
Name of the person performing the check
-
Serial or batch numbers of all components used
-
Signature of the person responsible for verification
The control process relies on printed production plans and a hardcopy Bill of Materials (BOM) generated from ERP systems like SAP. Component numbers on the production line are manually compared with those listed in the BOM. For components without serial numbers, verification is done based on packaging artwork. As additional proof of control, physical samples or uniquely identifying fragments of components are often glued into the KSM notebook.
Alternative KSM Practices in Modern Manufacturing
Some companies have introduced alternative, semi-manual approaches to the KSM process, such as:
-
Verifying each new batch of components before they’re loaded into production. Operators scan packaging codes from multiple containers before use
-
Checking device settings for marking equipment such as labelers or lasers that imprint product information on packaging
Challenges with Paper-Based KSM Documentation
Completed KSM notebooks are stored until the produced goods reach their expiration date (BBD). However, this traditional documentation method is:
-
Prone to errors
-
Time-consuming to manage
-
Difficult to archive and retrieve during audits
These limitations make a strong case for transitioning to digital solutions like eKSM, which improve accuracy, streamline processes, and support better long-term data management.