System
Our RFID Identification System offers automatic recognition and tracking of materials via RFID tags, leveraging strategically placed readers and antennas throughout production facilities. This system not only monitors the movement and sequence of materials but also tracks their duration at various production stages while gathering data from essential machine sensors. The collected information is transmitted to a central system for analysis, ensuring compliance with recipes and evaluating the correctness of processes and sub-product preparation.
This type of solution is particularly effective in processes where the same containers, tanks, or baskets are repeatedly used, especially in closed production cycles where materials do not leave the facility.
The technology is employed as an alternative solution for process monitoring in situations where scanning 1D and 2D codes is difficult or impossible to implement—for instance, due to extreme production conditions, such as very low temperatures in cold storage facilities (-22°C).
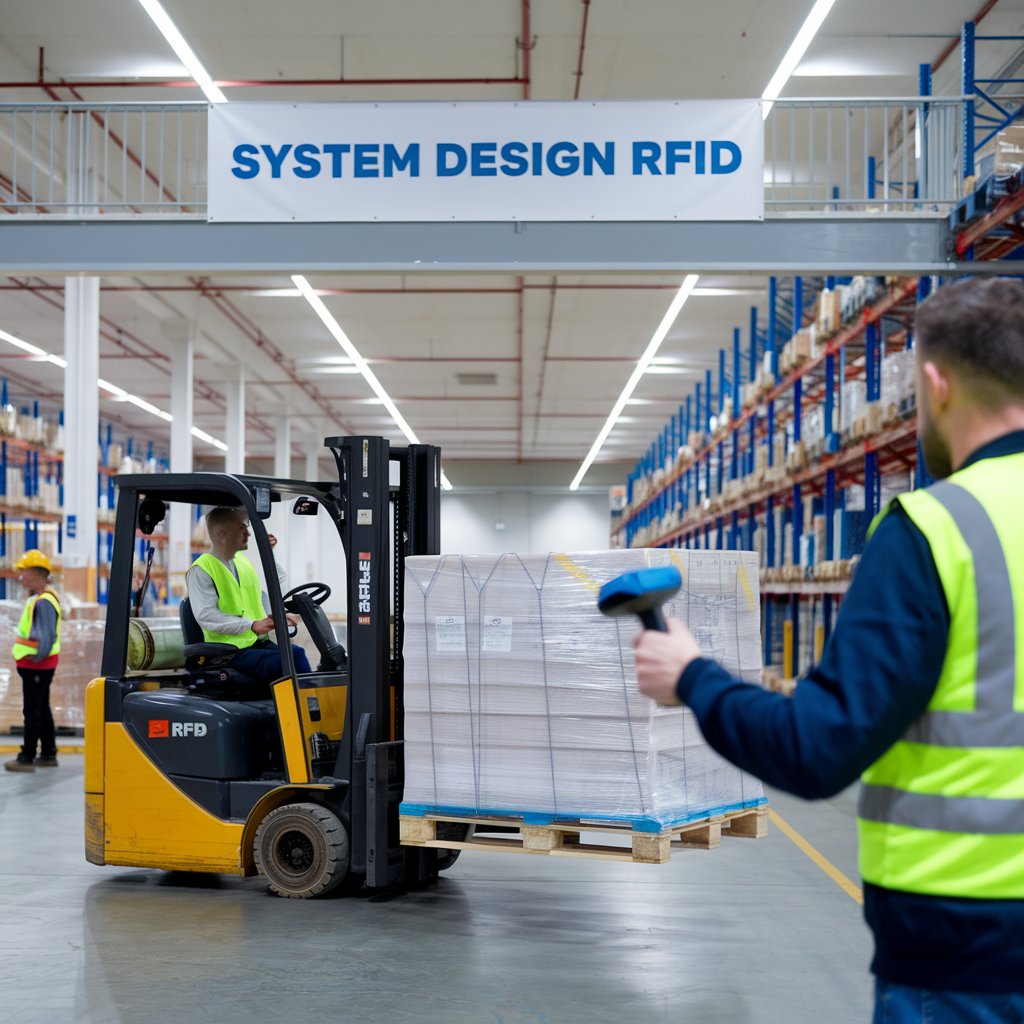
Case Study
At the client’s production facility, a semi-finished product is manufactured onsite. The raw material for its production is delivered to the plant, where it undergoes a complex technological process involving various treatment stages. During this process, the raw material is stored in reusable steel containers.
The production of the semi-finished product follows specific recipes that define the individual processing stages, machine settings, and the time the material must remain at each stage. The production process operates 24/7, with containers being handed over to operators on subsequent shifts depending on their processing stage.
The quality control department frequently encountered issues with improper execution of specific production stages, such as adding incorrect flavors, using incorrect machine settings, or prematurely ending the mixing process. Despite implementing employee training and paper-based reporting, mistakes continued to occur.
To address these issues, we introduced an RFID system to tag production containers. This technology allows for the reading of tags from a distance of approximately 1 meter, enabling precise identification of containers, including metal ones.
With the RFID solution, our system can reliably identify containers and monitor their compliance with recipes, time spent at each processing stage, sequence of operations, and the correctness of machine settings.
An added benefit of the system is the detailed statistics it provides on production times for each container. Within a short period, these insights helped identify bottlenecks in the process, enabling optimization and significantly improving efficiency.
RFID technology is particularly valuable in production facilities where precise verification of material flow between key points, such as workstations, storage areas, and production halls, is required, as demonstrated in this case.
Why Choose Our RFID System?
Our RFID technology is a robust solution for facilities that demand precise material tracking and process monitoring. From automating routine tasks to providing actionable insights for process optimization, this system drives operational excellence in even the most challenging production environments.