SmartVision System
The SmartVision System revolutionizes quality control by addressing recurring production challenges, including operator errors, incorrect components, machine wear, and marking equipment issues. Using advanced image processing, SmartVision monitors, analyzes, and assesses product quality in real-time. Key differentiators include its ability to identify long-term trends in quality defects and provide actionable insights.
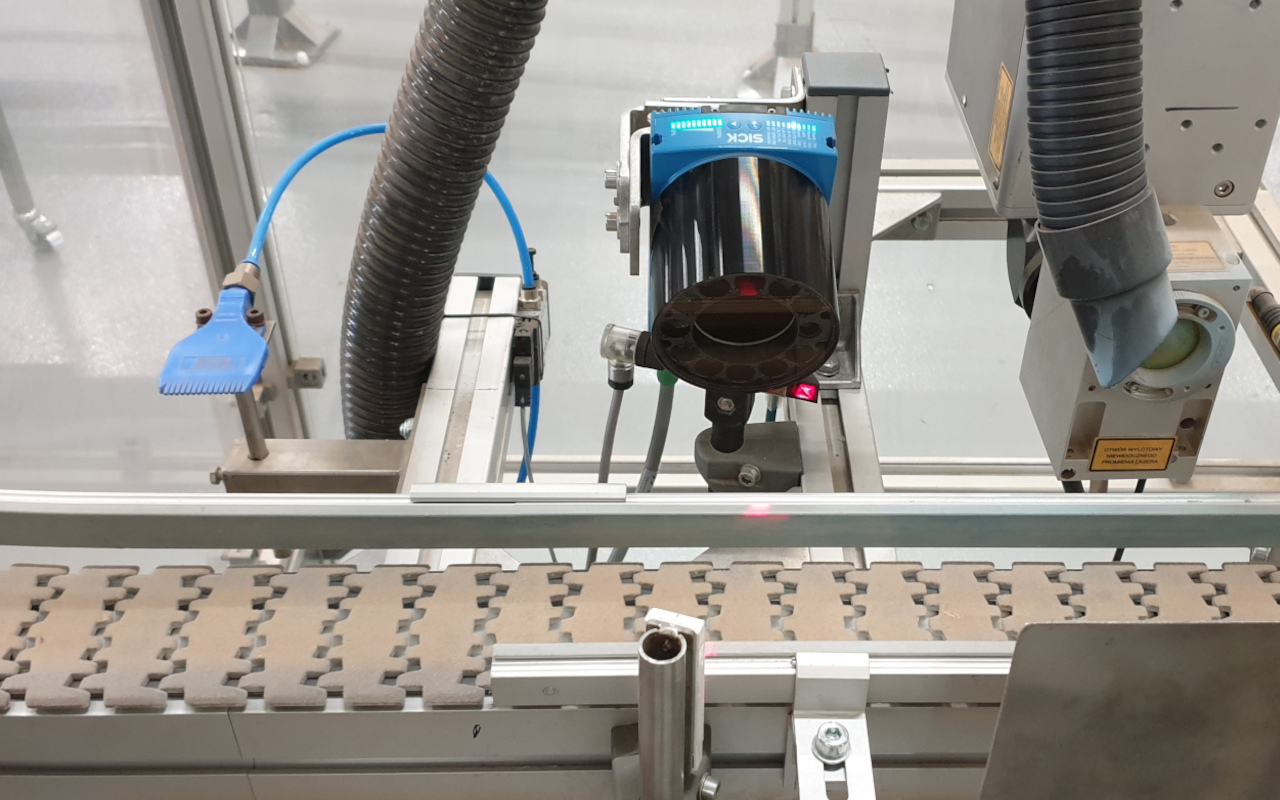
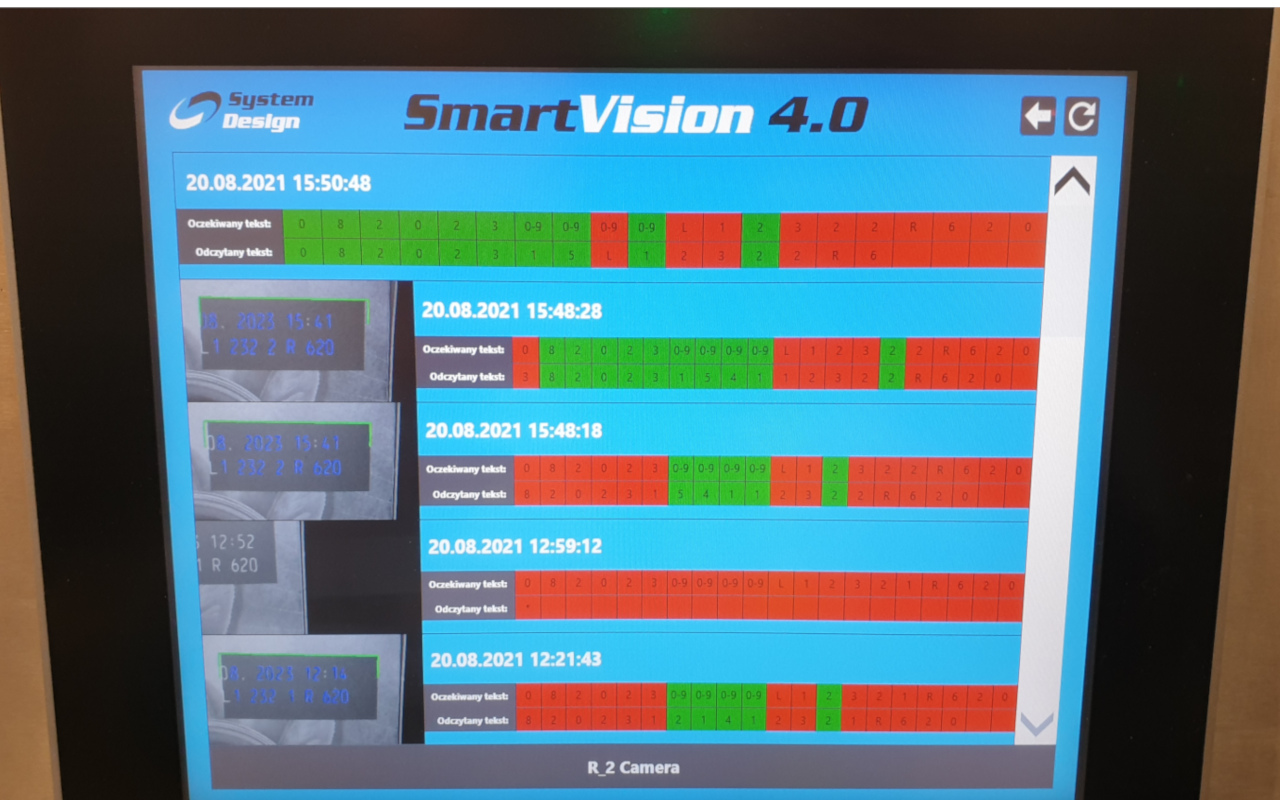
Our solution records and stores data on detected quality defects along with photos of the incidents, categorized into defined groups. The system makes this data accessible to employees via a web interface in an internet browser.
The quality department and plant management can receive real-time information about quality issues and analyze error occurrence trends over medium- and long-term periods.
Data can be reviewed and analyzed directly from a computer after logging in with the appropriate permissions. The system enables in-depth analysis and easy identification of the root causes of errors.
With access to this information, the quality department can analyze data over a specified period using defined parameters. Eliminating identified defects allows the department to achieve measurable savings by reducing the number of production rejections in the facility.
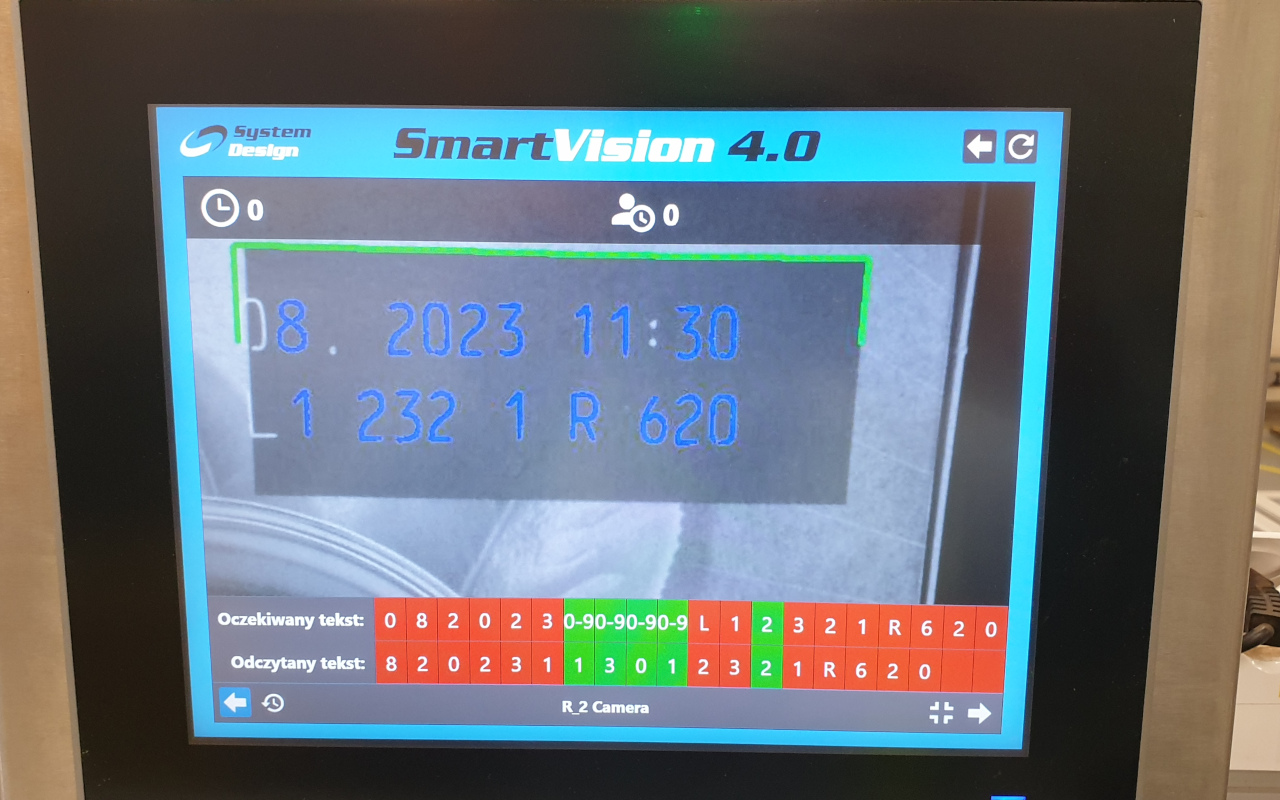
SmartVison
Business Benefits of SmartVision
Any questions?
Want to know more?
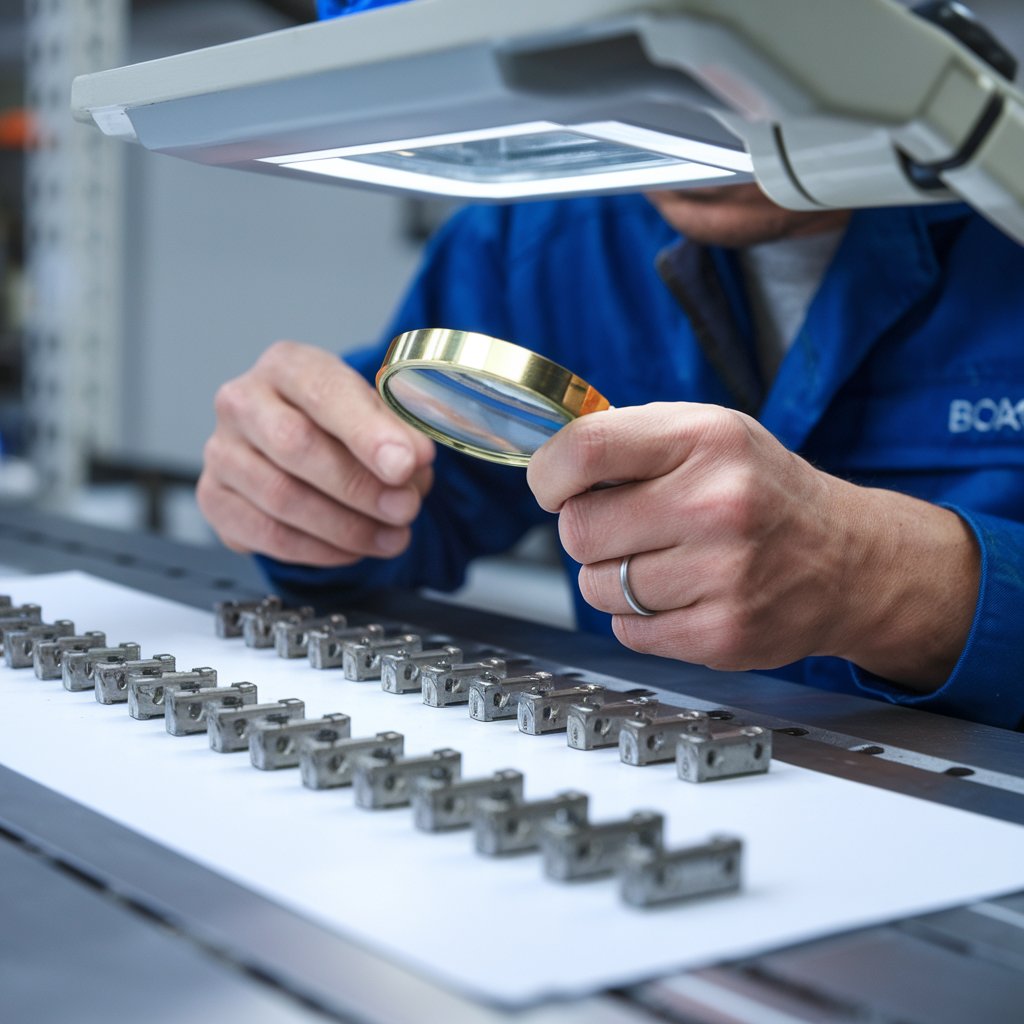
- Cost Reduction: Automates inspections, minimizing operational expenses.
- Error Mitigation: Detects defects with consistent accuracy, reducing undetected issues.
- Objective Quality Standards: Applies uniform criteria for product evaluation, ensuring reliability.
- Immediate Reporting: Alerts for defects allow rapid problem resolution.
- Fewer Returns and Complaints: Improves product quality, lowering customer dissatisfaction costs.
- Raw Material Savings: Early detection of subpar components prevents further losses.
- Enhanced Efficiency: Real-time data analysis avoids production slowdowns or stoppages.
- Downtime Reduction: Trends analysis predicts and prevents machine adjustments or servicing delays.
- Training Optimization: Reduces reliance on manual quality checks, easing workforce training requirements.
- Low Ownership Costs: Web-based interface eliminates the need for user-end software installations, simplifying updates.
- Advanced Reporting: Analyzes defect reasons, filters events by production line, product type, and time (graphs and statistics included).
- Camera Compatibility: Integrates with cameras from any manufacturer, supporting existing setups.
- Scalability: Accommodates numerous inspection cameras, consolidating data into one database.
- Flexible Inspection Rules: Easily adjusts patterns and criteria based on defined regulations.
- Error Data Storage: Archives defect details with corresponding images for thorough review.
- User-Friendly Interfaces:
- Operator view for recent defect reviews with images.
- Technician tools for in-depth troubleshooting.
- Quality Tools: Graphical analyses and trend detection for data-driven improvements.
- Web-Based Access: Requires no additional installations, streamlining use and maintenance.
Case Study
In an industrial facility, a vision inspection system was implemented to reduce labor costs associated with manually detecting product defects and faults. Standard systems check for quality errors at a specific point on the production line, monitoring the number of rejects within a given timeframe. When the number of rejects exceeds a set limit, a technician is automatically called to perform immediate adjustments on the line. However, the quality department observed that the standard system did not allow for trend analysis or pinpointing the root causes of errors at the level of individual incidents.
In the facility, a dedicated employee periodically monitored the number of rejects on each production line and, based on their experience, carried out ad hoc corrective actions. However, the quality department lacked full access to detailed information about the detected quality errors.
We proposed the installation of our Smart Vision Inspection System, which, in addition to standard functions, enables data collection and analysis of quality errors with full access for the quality department. The system allows data to be reviewed by categories such as time, SKU, shift, machine, component, and other quality error parameters.
Thanks to proactive monitoring and medium- and long-term trend analysis, the quality department quickly identified and resolved a significant quality issue. It was discovered that a laser used for marking products was performing poorly on one specific box color. Parts of the text, such as dots and the ends of letters, were illegible—an issue not observed on darker packaging from the same production line.
Without the ability to analyze reports and observe trends, identifying this problem would not have been possible.